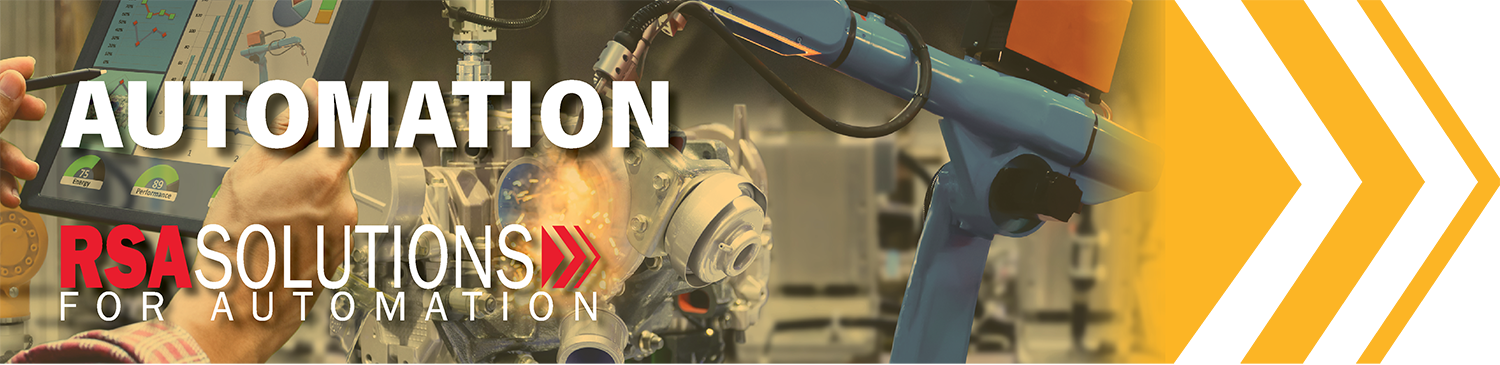
Case Study: Machine Center Controls Update
The Problem:
A company’s machining center had a control system that was 20 years old. The controls and drives were no longer operational, but the machine’s mechanics were still were able to operate within tolerance specifications. The customer decided that they would like to keep the machining center and fully replace the controls, motors, and drives.
MCE's automation team (RSA) took on the job of updating the old 11-axis machining center electrical enclosure. When they got their hands on the old electrical cabinet from the machine: it was 1,000 pounds of enclosure and covered in oil and dirt.
When the RSA team looked at the machining center, the drives were covered in oil and dirt and the wires were scattered, but the machine's mechanics were more functional--they could still operate within tolerance specifications and produce good parts.
The Solution:
The team cleaned the cabinet and provided a new back panel for the hardware. The cleaning phase took a lot of rubber gloves and solvent, but once they finished, the electrical cabinet looked like new.
RSA removed all of the old power components and replaced them with new ones. They designed a new panel layout, electrical schematic, created a new BOM, assembled and wired the panel, programmed the controller, and then commissioned the machine at the customer site.
The Omron controller was programmed to do the same work as the previous controller (the old Allen Bradley controller’s program was converted to the Omron PLC software), and the old drives and motors replaced by Yaskawa Sigma 5 Mechatrolink 2 servo drives and Sigma5 servo motors. The customer supplied the Omron controller and Yaskawa products.
Products used:
- Yaskawa- motors, drives, cables
- Wago- terminal blocks, power supplies, fuse holders
- Omron PLC with Motion Control
The Value:
Hiring MCE to rebuild the control center enclosure and replace the main control, motors, and drives allowed them to restore production capacity using an existing machine instead of purchasing a new machining center. Our customer saved money they would have spent purchasing a brand-new unit and the machining center looked and worked as good as new, and our customer was highly satisfied with the results.
Before
The old machining center wires were all over the place, covered in dirt, and the controls and drives were no longer operational.
After
When the RSA team completed the job, the machining center was clean and organized neatly and operated as good as new--saving our customer what they would have spent on a brand new control center.
To learn how our team can help you save by getting the automation job done, click to request a quote from us today.
Want to learn more?
Please click the button to the right and fill out an interest form so we can set up a quick call to discuss your specific application needs.